
Which pressure plates should be used for flat roofing?
- Read time: 4 minutes
- Date: 21 Jun 2021
- Flat Roofing
Normally tube washers and fasteners should be used for securing insulation and membrane. However, sometimes this is not practical, especially in refurbishment and cold roof applications where the depth of insulation is not sufficient to accommodate the spigot of the tube washer. In these instances, pressure plates should be used.
Which pressure plates should be used for which application?
Pressure plates are manufactured in various materials and sizes for different applications:
Materials:
Generally, pressure plates are manufactured from either stainless steel or carbon steel. Stainless steel offers the best resistance to corrosion and plates are either manufactured from A4/316 grade or A2/304 grade. The A4 grade offers the best protection against corrosion and this is the preferred grade for marine environments. All carbon steel pressure plates must be coated to resist corrosion.
Size:
Broadly speaking there are pressure plates for securing insulation and plates for membrane. When securing insulation, we recommend using a larger pressure plate with a diameter of at least 70mm. The larger size provides a greater bearing surface and is beneficial especially when securing foil-faced boards as it helps prevent damaging the foil. The IMA (Insulation Manufacturers Association) recommends this larger size for mechanically fixed insulation where the membrane is fully adhered – see IMA ID/1/2009.
When securing membrane, a smaller pressure plate is generally used. This is normally sited near the edge of the membrane and the next roll overlaps and conceals the fixing point. Membrane pressure plates are either round or oval. The oval plates offer the greatest resistance to wind uplift but round plates are easier to position.
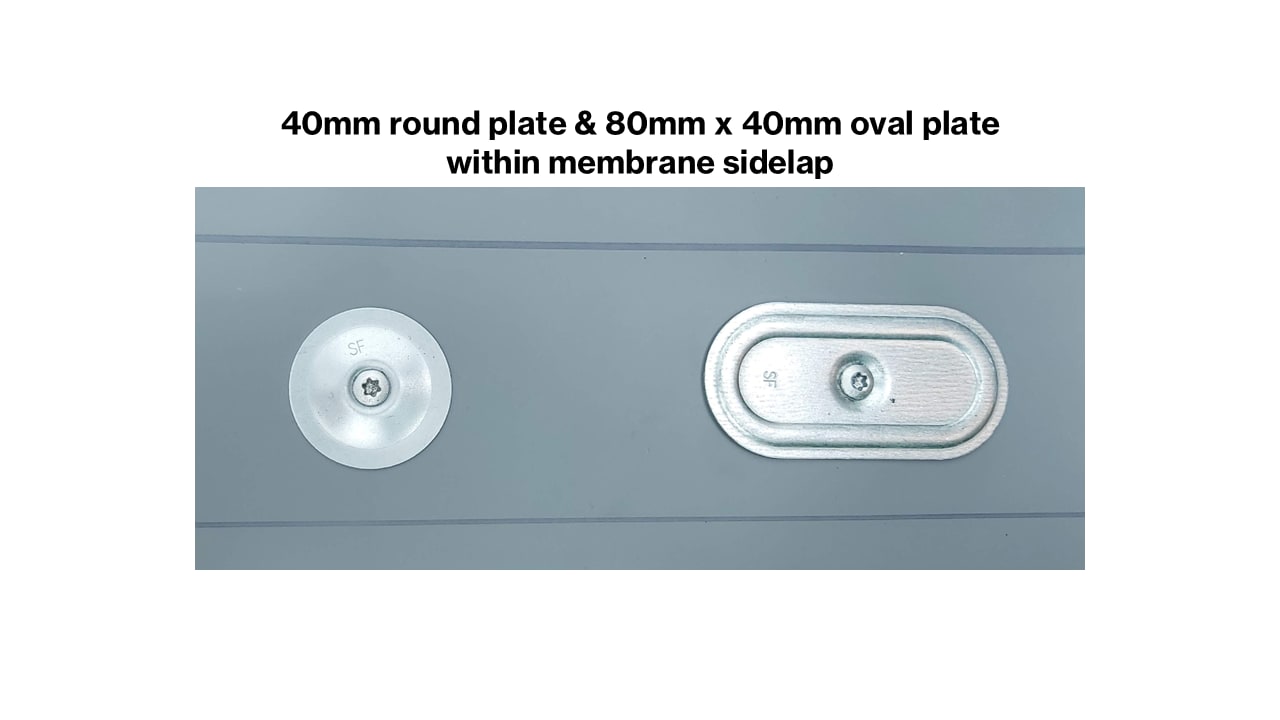
Round plates are generally between 40mm to 60mm in diameter. Some plates also have barbs to the underside, which grip the membrane providing greater wind uplift resistance.
(Different manufacturers will have their own guidance on what plates should be used for their specific systems.)
Profile:
Pressure plates are manufactured with different profiles, which provide their strength and rigidity. The profile used depends on the application. The most common profiles are flat, shallow dish or deep dish - the names refer to the underside shape of the pressure plate.
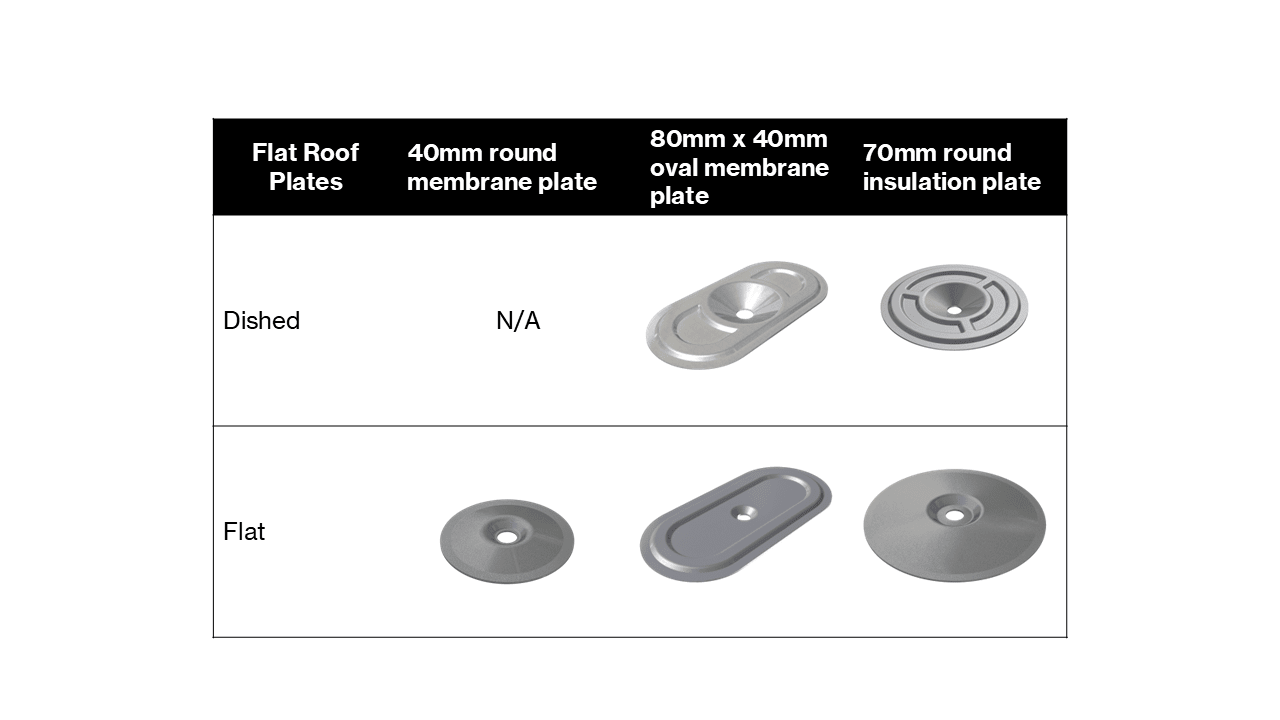
Flat pressure plates must be used when securing a membrane directly over a rigid surface such as plywood.
Shallow dish pressure plates must only be used when securing compressible insulation. The pressure plate works by sinking into the insulation slightly so the fastener head sits below the top of the plate. This prevents the fastener head from coming into contact with the membrane, which could damage the waterproofing over time.
Deep Dish pressure plates must be used to secure compressible insulation with a ‘hex’ head fastener. The deeper profile creates the space required to ensure there is no contact between the fastener head and the membrane.
It’s important to ensure that the pressure plate used has a sufficient hole diameter to accommodate the fastener.