
What is hydrogen embrittlement?
- Read time: 4 minutes
- Date: 25 Jan 2022
- Flat Roofing
- Rainscreen & Façades
- Sheeting & Cladding
This means hydrogen embrittlement can cause component failure without visible signs of deterioration.
Cases of hydrogen embrittlement are quite rare. It occurs when steel absorbs new unbonded hydrogen atoms during manufacture or processing. When a component, is placed under loading, these atoms move towards the areas of high stress, causing sub-microscopic cracking (cracks too small to see with an ordinary microscope).
Hydrogen embrittlement is self-perpetuating meaning that once it starts it will continue to get worse. The cracks create more areas of high stress and so the process repeats until they have spread throughout the material. This ultimately results in the failure of the component at loads below those it has been designed to withstand.
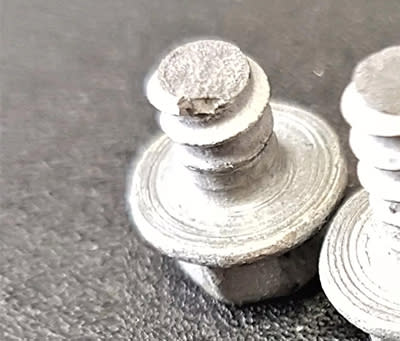
What metals are affected by hydrogen embrittlement?
The metals that are most vulnerable to hydrogen embrittlement are high-strength steels, titanium alloys and aluminium alloys.
What do manufacturers do to prevent hydrogen embrittlement?
The prevention of hydrogen embrittlement starts which the specification of the part and the manufacturing processes that it undergoes. A key cause of hydrogen embrittlement is the electroplating process which some fasteners undergo.
Acid pre-treatment and electroplating puts parts made from susceptible materials at risk of hydrogen embrittlement. Reputable fastener manufacturers will avoid these types of processes to reduce the risk they pose.
How is hydrogen embrittlement detected?
In the unlikely event that hydrogen embrittlement occurs, it usually happens very quickly after installation and within the first hour to 48 hours.
Hydrogen embrittlement can only be detected under laboratory conditions. Tests are carried out during the manufacturing and processing of components to ensure that hydrogen embrittlement has not occurred. These tests involve placing the fastener under high-stress loading over an extended period of time to ensure it does not fail. The loading is typically higher than it would be subjected to during the course of its normal life expectancy.
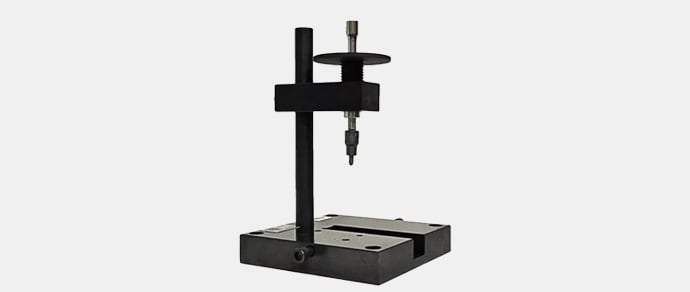
If a component or system fails on-site or in situ and hydrogen embrittlement is suspected, it is examined by the manufacturer and if required, an independent laboratory to detect the sub-microscopic cracking. Hydrogen embrittlement is rare, and most fastener failures are caused by using the wrong fastener for the application, environmental conditions or load.
Find out more about how to specify the correct fasteners
How does stress corrosion cracking differ from hydrogen embrittlement?
Stress corrosion cracking, also referred to as environmental hydrogen embrittlement (EHE), is a type of corrosion that occurs due to the introduction of hydrogen atoms to stainless steel through environmental factors. It is caused by contact with certain chemicals such as chlorine.
Learn more about stress corrosion cracking and how it affects fasteners