
Tooling guide for Rainscreen support systems
- Read time: 5 minutes
- Date: 12 Mar 2022
- Rainscreen & Façades
Using the wrong tools when fitting a rainscreen system can damage the fixings. And if they fail, it could have severe consequences for the installer. Using the right tools is essential to achieving an accurate result and will help speed up the drilling process.
Fixing into steel or aluminium
When fixing into a metal substrate it is likely you will be using a self-drilling fastener. There is specialist tooling available for this, see our guidance in our Skills Hub article below.
A guide to tooling for sheeting and cladding
Fixing into concrete and masonry
When fixing into concrete or masonry there are some key points to ensure that will ensure correct installation is achieved.
Before installing a concrete anchor, it will be necessary to drill a pilot hole. This hole should be approximately 20% longer than the embedment depth of the fastener to allow dust to be pushed past where the fastener is installed.
If chemical fixings such as resin, are being used it is important to clear the dust from the drill holes before using adhesive, otherwise fasteners bond to dust rather than the substrate. It is then essential to use a blow-out pump to remove as much dust as possible before pushing the fastener into the hole. When using chemical fasteners, it is important to follow the manufacturer's guidelines and allow the resin to bond for the specified time period. Applying load before the resin has cured is likely to result in fastener failure.
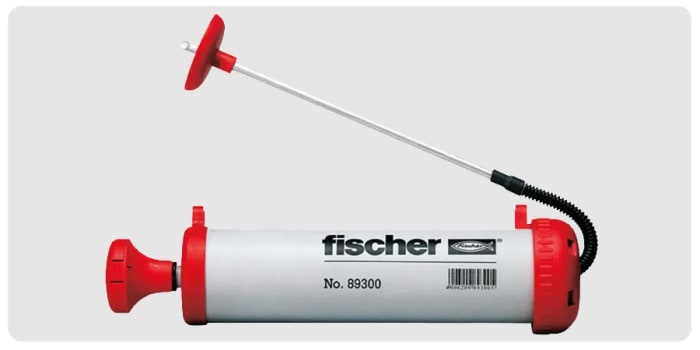
Preserving drill bits
Drill bits wear down the longer they are used, so the diameter gradually becomes smaller and smaller making it more difficult to push the fastener into the drill hole.
The rate of wear depends on a range of factors such as the drill type and speed, and the hardness of the substrate, but as a guide, we recommend changing drill bits regularly.
To help preserve the life of the drill bit, let the drill do the work. Placing pressure on the drill doesn’t speed up drilling but increases the speed of wear on the drill bit, so it will need to be replaced more quickly. Adding pressure to the drill can also cause the drill bit to bend, which creates an elongated hole, which could allow the fastener to move.
Always use the correct length of drill bit for the fastener – if you use a long drill bit for a short fastener, you will wear a long drill bit unnecessarily and over time could cause the drill bit to bend.
Always wear a mask
Always wear a mask when cutting, drilling, grinding and polishing construction materials such as bricks, tiles, concrete and mortar as this can create silica dust. Silica dust can cause respiratory problems, such as coughing and shortness of breath and in severe cases, lung cancer, silicosis and chronic obstructive pulmonary disease, which can lead to death.
For more information please refer to the following HSE guidance
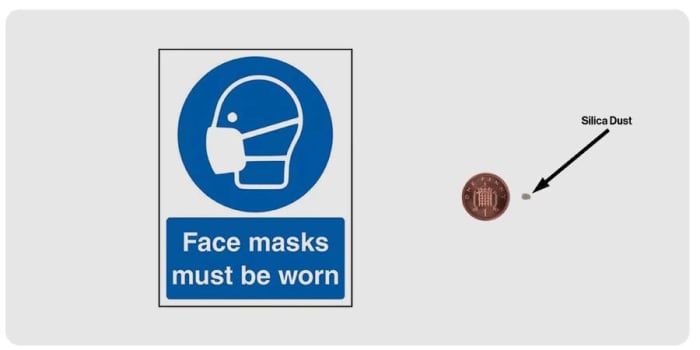
Use a calibrated torque wrench
Some mechanical anchors require installation with a torque wrench set to the manufacturers recommendations to ensure they are tightened correctly. Using a standard wrench or an uncalibrated torque wrench can lead to overtightening, which can crack the concrete or masonry substrate.
Using the right tooling will not only help you to achieve the best possible finish by ensuring you have driven the fasteners to the correct depth, but it will be much quicker too.
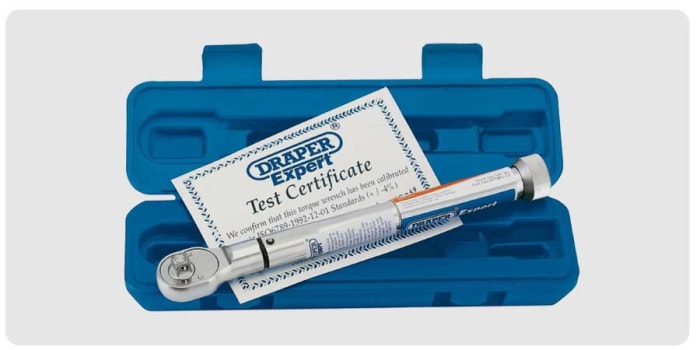