
Fixings and sealants for aluminium fabrications
- Read time: 4 minutes
- Date: 12 Feb 2022
- Rainscreen & Façades
- Sheeting & Cladding
The most important consideration when fixing into aluminium is thermal expansion and contraction due to temperature changes. If this isn’t factored into the design and installation, it can cause the fabrication and substructure to buckle, damage the fasteners or cause them to back out of the capping, all of which can lead to structural failure.
There are two fixing methods for aluminium fabrications; floating fix and dead fix.
Floating fix: each length of aluminium fabrication is secured with one dead fix (fixed point) to the substructure using one or a group of fasteners, usually positioned centrally. All other fixings feature oversized or slotted holes or a sliding clip to create a sliding or floating fix, which allows the aluminium to expand and contract freely. Oversized or slotted holes should not be used on the inner section of the fabrication or the substructure.
Thermal expansion of the aluminium fabrication will occur in every direction from the dead fix. The size of the expansion hole will vary depending on the colour of the fabrication (darker colours result in greater thermal expansion) and the position of the sliding fix to the dead fix – holes should increase in size as they move further from the fixed point. Calculations will also be affected by the temperature during installation. When installation takes place in cold weather, heat expansion should be allowed for, while cold contraction should be factored in when installation takes place in warm weather.
Fasteners should always be positioned in the middle of the expansion hole using a centring tool. An expansion gap must also be incorporated between panels or fabrications.
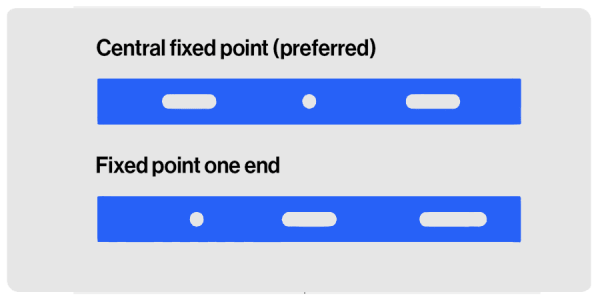
Dead fix: the entire length of each aluminium fabrication is secured to the substructure using a dead fix (fixed point). This means there is no allowance for thermal expansion and movement. Because of the potential for fixing or fabrication failure caused by thermal expansion, Finite Element Analysis of the application must be undertaken for each location. A dead fix methodology must not be undertaken without specialist design advice from the fabrication manufacturer.
When fixing into aluminium, it is recommended that fasteners should be used to secure fabrications to the substructure or sheeting at a maximum of 500mm centres. Do not fix aluminium fabrications into wall sheets or light gauge roof unless they have been specifically designed for this type of substrate.
When fixing aluminium flashings, fasteners should be positioned at a maximum of 500mm centres for verges and 400mm centres for fixing ridge and hip flashings. Use floating fix for lap and butt strap joints.
What type of fasteners should I use when fixing into aluminium?
Correct specification of fasteners is critical when fixing into aluminium. As with all rainscreen, cladding, sheeting or roofing projects, fasteners must have the necessary performance values to be able to withstand the forces, such as wind loading, they will be subjected to in the application.
What are fastener performance values?
A2 or A4 stainless steel self-drilling fasteners or rivets must be used when fixing into aluminium to prevent bi-metallic corrosion. For this reason, never use carbon steel fasteners.
What is bi-metallic corrosion?
If the correct fastener is not used, the fasteners can ‘unwind’ as the aluminium contracts and expands causing flashings and panels to become loose.
When using rivets, the correct pilot hole size is essential.
Where a waterproof seal is required, washers with a large circumference should be used to completely cover the oversized expansion holes.
How do you accommodate movement when using sealant?
A common problem when fixing aluminium using sealant is that the joint can be over compressed as fasteners are tightened. This squeezes the sealant out of the joint leaving just a thin film behind. While it may appear that the metal has bonded, this film can pull apart under loading as the metal expands and contracts causing the sealant to fail, resulting in leaks.
To prevent over compression, medium density compressed foam tape or shimmed preformed butyl strip sealant must first be bonded to one face of the joint to act as a spacer. The sealant should then be beaded alongside the spacer before the two metal surfaces are fixed into place. On a lap or butt joint, install fasteners at 75-100mm centres to ensure a reliable, durable weatherproof seal is formed.
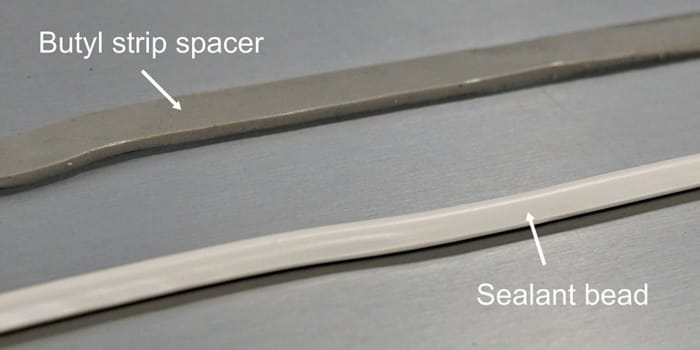